Cable Installation: Maximum Allowable Pulling Tension and Safe Handling Guidelines
Master cable installation with expert guidance on maximum allowable pulling tension and safe handling guidelines—formulas, best practices, and compliance tips for reliable, damage-free pulls.
Cable Installation: Maximum Allowable Pulling Tension and Safe Handling Guidelines
Introduction
In industrial settings, proper cable installation can mean the difference between reliable system performance and costly downtime. Among the critical parameters governing successful installations, maximum allowable pulling tension stands as perhaps the most important yet frequently misunderstood factor. Whether you're installing power distribution systems in manufacturing facilities, data cables in commercial buildings, or specialized wiring in infrastructure projects, exceeding the appropriate tension limits can lead to immediate damage or premature failure.
This comprehensive guide explores the science behind cable pulling tensions, provides practical calculation methods, and delivers actionable safe handling guidelines that industry professionals can implement immediately. Engineers, technicians, and project managers will find the technical guidance necessary to ensure installations meet both industry standards and project-specific requirements.
Fundamental Concepts and Terminology
Before diving into specific calculations, it's essential to establish a clear understanding of the key concepts that govern cable pulling operations.
Pulling Tension vs. Breaking Strength
Pulling tension refers to the longitudinal force applied to a cable during installation. This differs significantly from breaking strength, which represents the tension at which physical failure occurs. Safe installations always maintain substantial margins between these values, typically operating at no more than 40-60% of breaking strength.
Conductor Cross-Sectional Area (A) and Material Factor (K)
Cable engineering calculations rely heavily on two primary variables:
Cross-sectional area (A): Measured in square millimeters (mm²) for metric units or thousands of circular mils (kcmil) in imperial units
Material factor (K): A coefficient that accounts for the tensile properties of the conductor material
These parameters form the foundation of all pulling tension calculations and vary substantially across different cable types and applications.
Units and Conventions
Standardizing units prevents dangerous calculation errors. This guide uses:
Force: newtons (N) and kilonewtons (kN) in metric; pounds (lb) in imperial
Area: square millimeters (mm²) in metric; thousands of circular mils (kcmil) in imperial
Stress: newtons per square millimeter (N/mm²) or megapascals (MPa) in metric; pounds per kcmil (lb/kcmil) in imperial
Maximum Allowable Pulling Tension: Industry Guidelines
The maximum allowable pulling tension represents the lowest value calculated from applicable guidelines unless otherwise specified by the cable manufacturer. This conservative approach ensures safety margins accommodate real-world variables during installation.
Individual Conductor Limit
For single conductors, the maximum tension should not exceed:
Tcond = K · A
Where:
Tcond is the maximum allowable pulling tension on an individual conductor, in newtons (pounds)
A is the cross-sectional area of each conductor in square millimeters (mm²) or kcmil
K equals:
70 N/mm² (8 lb/kcmil) for annealed copper and hard aluminum
52.5 N/mm² (6 lb/kcmil) for ¾ hard aluminum
This formula accounts for the fundamental tensile strength properties of the conductor material while providing an appropriate safety margin.
Group Pull Limits
When installing multiple conductors simultaneously, different constraints apply:
Two to Three Conductors of Equal Size
When pulling two or three conductors of equal size together, the maximum tension should not exceed:
Tmax = 2 · Tcond
This limitation acknowledges that pulling stress distributes unevenly across bundled conductors, with outer conductors typically bearing more load than inner ones.
More than Three Conductors of Equal Size
For installations involving more than three conductors, the formula becomes:
Tmax = 0.6 · N · Tcond
Where:
N is the number of conductors
The 0.6 coefficient accounts for increased friction and non-uniform stress distribution across larger bundles
Special Grip Methods
The attachment method used to pull cables introduces additional constraints:
Eye-Type Pulling
When using a pulling eye, maximum tensions are strictly limited:
Single-conductor cable: 22.2 kN (5000 lb)
Two or more conductors: 26.7 kN (6000 lb)
Consult the cable manufacturer when installations might exceed these limits.
Basket Grip (Non-Lead Jacket)
For standard non-leaded jacketed cables pulled with basket grips:
Maximum tension: 4.45 kN (1000 lb)
This lower limit protects the jacket integrity, which can be compromised by the gripping mechanism itself.
Basket-Weave Grip (Lead Sheath)
Lead-sheathed cables require special consideration:
Tmax = Ka × π (D – t)
Where:
t is the lead sheath thickness, in millimeters (inches)
D is the outside diameter of lead sheath, in millimeters (inches)
Ka is the maximum allowable pulling stress in MPa, ranging from 10.34 MPa to 1.38 MPa (1500 to 200 psi) depending on the lead alloy
For lead-sheathed cables with neoprene jackets, a simplified limit applies:
Maximum tension: 4.45 kN (1000 lb)
Manufacturer Overrides and Specialty Cables
Specialized cables such as coaxial, triaxial, and other purpose-built designs typically have unique pulling requirements. Always follow the manufacturer's specific recommendations for these cable types, as standard calculations may not account for their particular construction.
Calculation Methods: Step-by-Step Guidance
Applying these formulas correctly requires a systematic approach:
1. Determine Conductor Area and Material Factor
First, identify the precise cross-sectional area and material composition of your conductors:
For standard sizes, refer to manufacturer specifications
For custom installations, measure directly or consult engineering documentation
Select the appropriate K-value based on conductor material (70 N/mm² for copper/hard aluminum or 52.5 N/mm² for ¾-hard aluminum)
2. Select Appropriate Formula for Conductor Count and Grip Type
Based on your installation configuration:
Calculate individual conductor limits (Tcond = K · A)
Apply the appropriate multiplier based on conductor count (2× for 2-3 conductors; 0.6 × N for 4+ conductors)
Check against grip-specific limitations (eye-type, basket grip, or basket-weave)
3. Unit Conversion Best Practices
To prevent dangerous calculation errors:
Maintain consistent units throughout all calculations
When converting between systems, use precise conversion factors:
1 N ≈ 0.225 lb
1 mm² ≈ 1.974 kcmil
1 MPa = 1 N/mm²
4. Margin and Safety Factors: Why "Minimum of All Limits" Matters
The final maximum allowable pulling tension is always the lowest value calculated from all applicable methods. This conservative approach ensures adequate safety margins for:
Unexpected obstructions
Uneven conduit surfaces
Variation in lubricant effectiveness
Imperfect alignment during installation
Safe Handling Guidelines
Calculating appropriate tension limits represents only one aspect of proper cable installation. These handling practices ensure successful execution:
Pre-Pull Inspection
Before beginning any pull:
Examine cable reels for damage or deformation
Verify cable jacket/sheath integrity along accessible sections
Inspect pulling grips for wear, proper sizing, and secure attachment
Check conductor ends for insulation damage or exposed metal
Lubrication: Selecting and Applying Pulling Compounds
Proper lubrication can reduce pulling tension by 50% or more:
Select lubricants compatible with cable jacket material
Apply lubricant continuously during long pulls
Use approximately 3-5 gallons per 1000 feet for power cables
Ensure even distribution, particularly at bends and pull boxes
Equipment Setup: Capstans, Pulleys, Tension Meters
Proper equipment configuration dramatically impacts pulling success:
Position pulleys at all direction changes
Ensure pulley diameter meets minimum bend radius requirements
Install tension meters at strategic monitoring points
Verify capstan capacity exceeds maximum expected tensions
Real-Time Tension Monitoring and Control
Active management during installation prevents damage:
Monitor tension continuously at pulling head or capstan
Implement predetermined stop points if tension approaches 80% of calculated limits
Adjust pulling speed based on real-time tension readings
Document peak and sustained tension values throughout the pull
Environmental and Site-Specific Considerations
Adapt installation approach to specific conditions:
Adjust techniques for extreme temperatures (below 40°F or above 100°F)
Implement additional controls for wet or submerged installations
Take special precautions at elevation changes exceeding 30 feet
Account for vibration in industrial settings or near heavy machinery
Material and Grip Selection
The interplay between cable materials and pulling methods significantly impacts allowable tensions.
Conductor Materials: Copper, Aluminum, Specialty Alloys
Different conductor materials exhibit distinct tensile properties:
Copper: High conductivity with excellent tensile strength (70 N/mm²)
Hard Aluminum: Lighter weight with good tensile properties (70 N/mm²)
¾-Hard Aluminum: More economical but reduced tensile strength (52.5 N/mm²)
Specialty Alloys: Used in high-temperature or corrosive environments (consult manufacturer)
Jacket Types: PVC, PE, XLPE, Neoprene, Lead Sheath
Cable jackets directly influence appropriate pulling methods:
PVC (Polyvinyl Chloride): Common, economical, moderate tensile strength
PE (Polyethylene): Higher tensile strength, good moisture resistance
XLPE (Cross-linked Polyethylene): Superior temperature performance, excellent tensile properties
Neoprene: Superior resistance to oils and chemicals
Lead Sheath: Special handling required, subject to creep under sustained tension
Grip Designs: Eye, Basket, Swivel, Custom Solutions
Select pulling attachments based on specific installation requirements:
Eye Grips: Direct connection to conductor, highest tension capacity
Basket Grips: Wire mesh sleeve over jacket, moderate tension capacity
Swivel Connections: Prevents cable twisting during pull
Custom Solutions: Manufacturer-designed for specialty applications
Installation Best Practices
Strategic planning significantly reduces installation difficulties and potential cable damage.
Route Planning: Bend Radius, Conduit Layout, Pull Boxes
Before beginning installation:
Verify minimum bend radius requirements (typically 8-12× cable diameter)
Ensure conduit size provides adequate fill ratio (25-40% depending on application)
Position pull boxes at appropriate intervals (generally every 100-150 feet for 90° bends)
Consider staged pulls for complex routes with multiple direction changes
Tension Control Strategies: Manual vs. Automated Systems
Different installations require appropriate tension management approaches:
Manual Control: Suitable for short, straightforward pulls with constant supervision
Semi-Automated: Tension monitoring with manual adjustment of pulling speed
Fully Automated: Computerized systems that adjust tension dynamically and halt operations if limits are approached
Team Coordination: Communication Protocols During Pull
Clear communication prevents mistakes:
Establish explicit hand signals or radio commands for start/stop/slow
Position personnel at critical points (feed reel, major bends, pulling end)
Implement clear chain of command for decision-making during complications
Practice emergency stop procedures before beginning
Record-Keeping: Pull Logs, Photos, Tension Profiles
Comprehensive documentation protects all stakeholders:
Record maximum and average tension values
Document pull speed and duration
Photograph completed installation at key junction points
Note any deviations from planned procedures
Worked Examples and Case Studies
Example 1: Single-Conductor Copper Cable (16 mm²)
Cable specifications:
16 mm² annealed copper conductor
PVC jacket
Eye-type pulling grip
Step 1: Calculate individual conductor limit Tcond = K · A = 70 N/mm² × 16 mm² = 1,120 N
Step 2: Check against grip-specific limits Eye-type pull limit = 22.2 kN (5,000 lb)
Step 3: Determine maximum allowable pulling tension Tmax = Minimum of (1,120 N, 22,200 N) = 1,120 N
Example 2: Four-Core Aluminum Group Pull
Cable specifications:
Four 240 mm² ¾-hard aluminum conductors
XLPE insulation
Basket grip attachment
Step 1: Calculate individual conductor limit Tcond = K · A = 52.5 N/mm² × 240 mm² = 12,600 N per conductor
Step 2: Apply multi-conductor formula (N > 3) Tmax = 0.6 · N · Tcond = 0.6 × 4 × 12,600 N = 30,240 N
Step 3: Check against grip-specific limits Basket grip limit = 4,450 N Multi-conductor eye limit = 26,700 N
Step 4: Determine maximum allowable pulling tension Tmax = Minimum of (30,240 N, 4,450 N, 26,700 N) = 4,450 N
Example 3: Basket-Weave on Lead-Jacketed Cable
Cable specifications:
Lead-sheathed cable
Outside diameter (D) = 35 mm
Sheath thickness (t) = 2.5 mm
Lead alloy with Ka = 5.17 MPa (750 psi)
Step 1: Calculate using lead sheath formula Tmax = Ka × π × (D - t) = 5.17 MPa × π × (35 mm - 2.5 mm) = 5.17 N/mm² × π × 32.5 mm = 528 N
Step 2: Check against standard limit for lead-sheathed cables Standard limit = 6,670 N
Step 3: Determine maximum allowable pulling tension Tmax = Minimum of (528 N, 6,670 N) = 528 N
Common Pitfalls and Troubleshooting Tips
Avoid these frequent installation errors:
Incorrect Area Calculation: Double-check conductor dimensions and use appropriate formulas for non-circular conductors
Lubrication Failure: Insufficient lubrication can double or triple actual pulling tension
Ignored Bend Factors: Each 90° bend can increase tension by 30-50% at the pulling end
Temperature Effects: Cold cables (below 32°F/0°C) may require tension reductions of 15-25%
Inspection, Testing, and Maintenance
Post-installation procedures ensure long-term reliability.
Post-Pull Inspection
After completing the pull:
Visually inspect jacket for abrasions, cuts, or deformation
Check cable ends for signs of conductor movement or telescoping
Verify proper seating in termination points
Measure insulation resistance before energizing
Tension Meter Calibration and Validation
Maintain equipment accuracy:
Calibrate tension monitoring devices annually
Verify calibration before critical installations
Document calibration dates and certification information
Compare readings across multiple devices when possible
Periodic Re-Tension Checks for Long-Term Installations
For permanent installations, especially vertical runs:
Schedule visual inspections at 1-year intervals
Look for signs of jacket creep or conductor displacement
Monitor termination points for evidence of movement
Re-secure supports if tension changes are observed
Documentation and Audit Trails for Quality Assurance
Maintain comprehensive records:
Archive all pull logs and tension data
Document inspection results and remedial actions
Cross-reference installation data with any subsequent performance issues
Retain records for the life of the installation
Conclusion and Recommendations
Proper application of maximum allowable pulling tension calculations and adherence to safe handling guidelines directly impacts both immediate installation success and long-term system reliability. The formulas and methods outlined in this guide represent industry best practices that help protect both personnel and assets during critical infrastructure installations.
The technical complexity of modern cable systems continues to increase, with specialized applications demanding ever more precise installation techniques. Feichun Cable's engineering team specializes in developing custom solutions for challenging installations, providing both technical guidance and purpose-built cable designs optimized for specific applications.
For projects requiring specialized support or custom-engineered cable solutions, contact Feichun Cable's technical services department. Our experienced engineers can provide tailored installation recommendations, on-site consultation, and project-specific tension calculations to ensure your next installation proceeds smoothly and reliably.
Appendix B: Glossary of Terms
Pulling Tension: Longitudinal force applied to cable during installation
Breaking Strength: Maximum tension a cable can withstand before physical failure
Conductor: Current-carrying component of a cable system
Jacket/Sheath: Outer protective covering of a cable
kcmil: Thousand Circular Mils, imperial unit of cross-sectional area
Pulling Eye: Device attached directly to conductor for pulling
Basket Grip: Wire mesh device that grips cable jacket during pulling
Appendix C: Quick-Reference Pull-Tension Calculator Workflow
Identify Cable Specifications
Conductor material (copper, aluminum, etc.)
Cross-sectional area (mm² or kcmil)
Number of conductors
Jacket/sheath type
Select Appropriate Formulas
Individual conductor: Tcond = K · A
Group pull: Tmax = 2 · Tcond or Tmax = 0.6 · N · Tcond
Special case: Tmax = Ka × π (D - t) for lead-sheathed
Apply All Relevant Limits
Material-based calculation
Grip-specific constraints
Manufacturer recommendations
Select Lowest Calculated Value
Document as maximum allowable pulling tension
Apply additional safety factor for critical installations

Frequently Asked Questions (FAQ)
What defines the maximum allowable pulling tension?
It is the lowest calculated value from all applicable tension limits (individual conductor, group pulls, grip methods), unless the cable manufacturer specifies otherwise .How do I calculate the tension limit for a single conductor?
Use Tcond=K×AT_{cond}=K \times AT cond=K×A, where AAA is the conductor’s cross-sectional area and KKK is the material factor .What is the material factor KKK for annealed copper?
K=70 N/mm2K = 70\ \mathrm{N/mm}^2K=70 N/mm2 (equivalent to 8 lb/kcmil) for annealed copper and hard aluminum .What is the material factor KKK for ¾-hard aluminum?
K=52.5 N/mm2K = 52.5\ \mathrm{N/mm}^2K=52.5 N/mm2 (6 lb/kcmil) for ¾-hard aluminum .How is the pulling tension calculated when pulling two or three conductors together?
Tmax=2×TcondT_{max} = 2 \times T_{cond}Tmax=2×Tcond to account for uneven load distribution in small bundles .How do I calculate tension for more than three conductors of equal size?
Tmax=0.6×N×TcondT_{max} = 0.6 \times N \times T_{cond}Tmax=0.6×N×Tcond, where NNN is the conductor count .What is the maximum tension with a pulling eye on a single-conductor cable?
22.2 kN (5 000 lb) when using a standard eye grip .What is the pulling-eye limit for two or more conductors?
26.7 kN (6 000 lb) for multi-conductor pulls; consult the manufacturer if higher tension is needed .What is the maximum tension for a basket grip on non-leaded cable?
4.45 kN (1 000 lb) to protect the jacket from mesh-induced damage .How is tension calculated for a basket-weave grip on lead-sheathed cable?
Tmax=Ka×π (D−t)T_{max} = K_a \times \pi \,(D - t)Tmax=Ka×π(D−t)
where DDD is lead OD, ttt is sheath thickness, and KaK_aKa (1.38–10.34 MPa) depends on lead alloy .
What if a lead-sheathed cable has a neoprene jacket?
The basket-weave limit defaults to 4.45 kN (1 000 lb) to protect the neoprene layer .When should I consult the manufacturer’s pulling recommendations?
For any special cable types (coaxial, triaxial, instrumentation) or if calculated tensions exceed standard limits .What is a jam ratio and why does it matter?
It’s D/dD/dD/d (conduit ID to cable OD). Ratios below 3.0 risk jamming during bends, causing physical damage .How do I calculate the jam ratio?
Divide the conduit’s inside diameter by the cable’s outside diameter: D/dD/dD/d .What is the maximum conduit fill percentage?
40 % per conduit section; higher fill increases friction and risk of overheating or jamming .Why is limiting conduit fill important?
It ensures space for cable movement, prevents excessive friction, and maintains allowable tension throughout the pull .How is tension in a straight conduit run calculated?
Tout=Tin+L×m×g×f×cT_{out} = T_{in} + L \times m \times g \times f \times cTout=Tin+L×m×g×f×c where LLL is length, mmm mass per length, fff friction, ccc weight factor .What friction coefficients are typical?
Dry PVC duct: f≈0.5f\approx0.5f≈0.5; lubricated: f≈0.2f\approx0.2f≈0.2 for significant tension reduction .How can I reduce friction during pulling?
Apply compatible cable-lubricant continuously, especially at bends and pull boxes, to lower fff and protect the jacket .How is tension through a horizontal 90° bend calculated?
Use the simplified bend formula Tout=Tin e(fcθ)T_{out}=T_{in}\,e^{(f c \theta)}Tout=Tine(fcθ) with θ\thetaθ in radians .How do I calculate tension through a vertical bend?
The same exponential bend formula applies, accounting for additional weight from vertical displacement .What should I do if calculated tension exceeds the allowable limit for a section?
Reverse pull direction, remove unnecessary bends, or redesign the raceway as demonstrated in Example H→A .Is there a rule of thumb for total bend angles in a pull?
Do not exceed 360° of cumulative bends without recalculating tensions; more bends amplify frictional effects .Where should I locate pull points or manholes?
At points where expected tensions exceed either pulling-tension or sidewall-pressure limits .Why is pre-pull inspection essential?
Verifying reel integrity, jacket condition, and grip security prevents damage under load .What are best practices for cable reel storage?
Store reels upright on solid ground, seal cable ends against moisture, and protect from UV if outdoors .Why must cable ends be sealed before pulling?
To prevent moisture or contamination ingress that can degrade insulation and conductor performance .How do I remove water from a flooded cable?
Apply vacuum or purge with dry nitrogen, then test for dryness before tension testing .Why adhere to the minimum bending radius during pulling?
Exceeding bend limits causes conductor deformation, insulation cracks, and early failure .How is the maximum pulling tension determined when mixed cable sizes share a raceway?
Use the effective area method: Tmax=K×AeffT_{max}=K\times A_{eff}Tmax=K×Aeff as per Annex O’s Equation O.1 .What is the “effective area” concept for multi-size pulls?
AeffA_{eff}Aeff sums each cable’s area multiplied by its grouping factor fff to reflect combined load .What maximum tension applies to fiber-optic cable pulls?
Ranges from 200 N to over 3 000 N depending on construction—always confirm with the fiber cable manufacturer .How is fiber-optic pull tension calculated?
Identical to metallic cables: account for cable weight, conduit geometry, and frictional coefficients .Why do fiber-optic installations require special lubricants?
Long pulls and low-mass cables demand lubricants that remain evenly distributed in the duct .What minimum bending radius should I use for fiber-optic cables?
Typically 20× the cable diameter to prevent micro-bending losses and fiber damage .
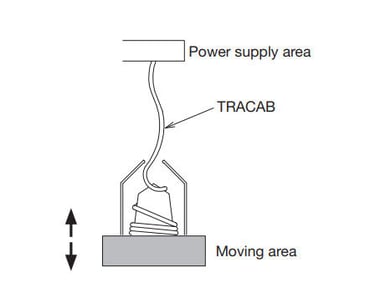

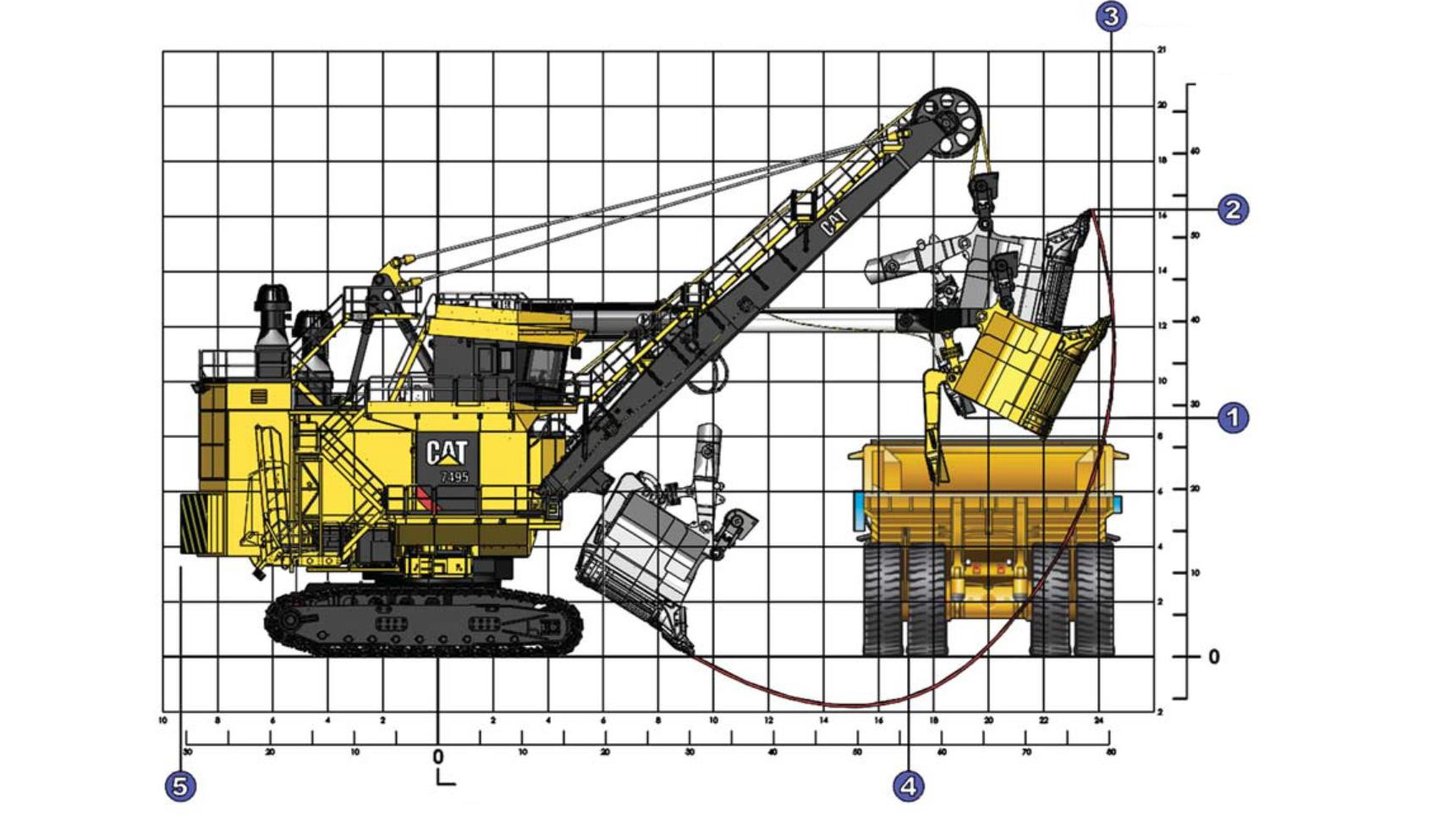
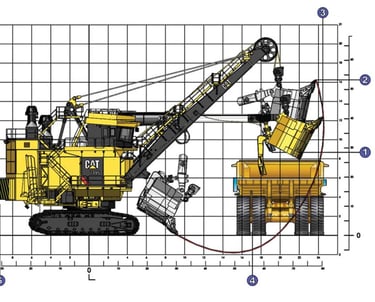
Cable Installation: Maximum Allowable Pulling Tension and Safe Handling Guidelines
Master cable installation with expert guidance on maximum allowable pulling tension and safe handling guidelines—formulas, best practices, and compliance tips for reliable, damage-free pulls.
5/1/202512 min read