Reeling Cable Solutions
Explore flexible power cables for mobile machinery in port terminals and shipyards. Technical insights await.
Mining Cutting Machines: Technology and Cable Installation Requirements
Ensure optimal performance and longevity of your mining equipment with expert insights on Types of Mining Cutting Machines and tailored trailing cable solutions—covering abrasion resistance, flex life, tensile management, and EMI shielding for every application.
Mining Cutting Machines: Technology and Cable Installation Requirements
In the demanding world of modern mining operations, cutting machines represent the critical interface between raw earth and mineral extraction. These sophisticated systems transform the ancient practice of mining into a precise science, but their effectiveness relies heavily on robust power delivery systems—particularly trailing cables that must withstand extreme conditions. This article explores the diverse landscape of mining cutting technologies and the specialized cable requirements that keep these mechanical giants operational.
The Critical Role of Trailing Cables
Trailing cables serve as the lifeline for mobile mining equipment, delivering electrical power while accommodating continuous movement. Unlike fixed industrial installations, these specialized cables face unique challenges:
Constant flexing as machines maneuver through mining environments
Abrasion against rock surfaces and machine components
Impact damage from falling debris and rock fragments
Environmental exposure to moisture, dust, and corrosive materials
Temperature fluctuations from ambient conditions and motor heat
A well-designed trailing cable must balance electrical performance with mechanical durability, featuring optimized tensile strength, insulation integrity, and minimum bending radius specifications tailored to specific machine applications.
Major Classes of Mining Cutting Machines
1. Continuous Miners
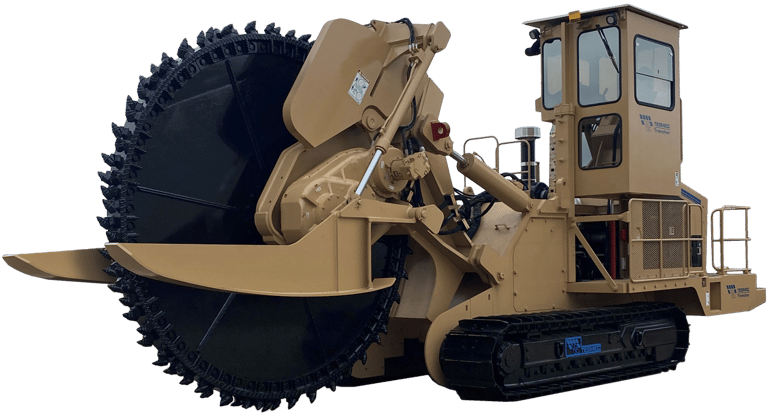
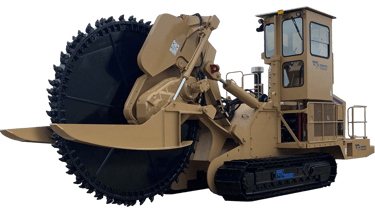
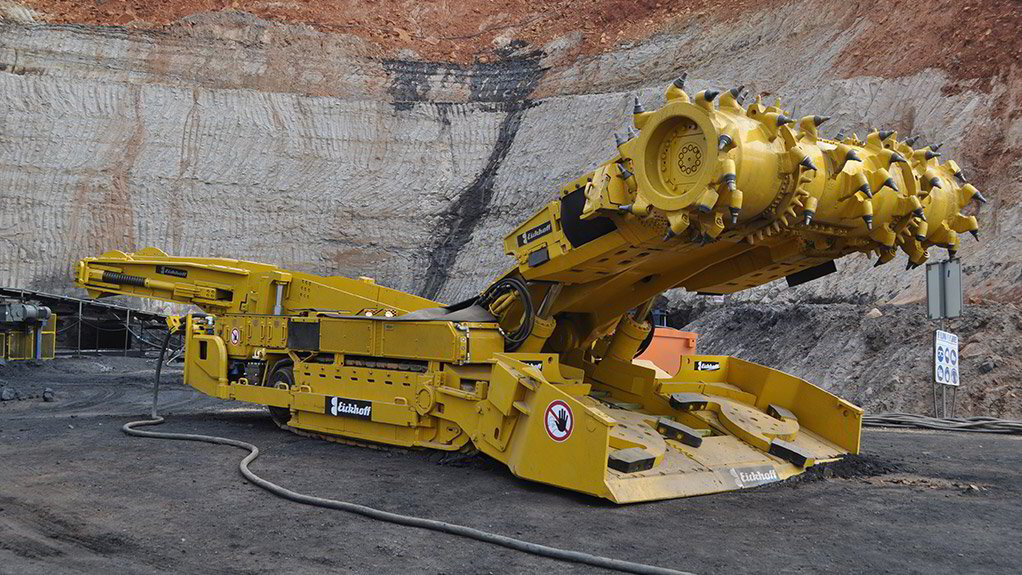
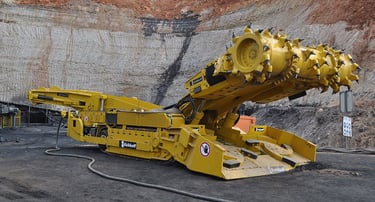
Purpose: These versatile machines simultaneously cut, gather, and load material in underground mining operations.
Technical Features:
High-torque rotating drum with carbide-tipped cutting bits
Integrated conveyor system for immediate material removal
Compact design for tight-radius operation in confined spaces
Cable Requirements:
Enhanced flex life for continuous operation
Abrasion-resistant jacketing at identified wear points
Robust strain relief to handle frequent direction changes
Fire-resistant compounds for coal mine environments
Application Focus: Coal mining, potash extraction, salt mining, and other soft mineral operations.
2. Roadheaders
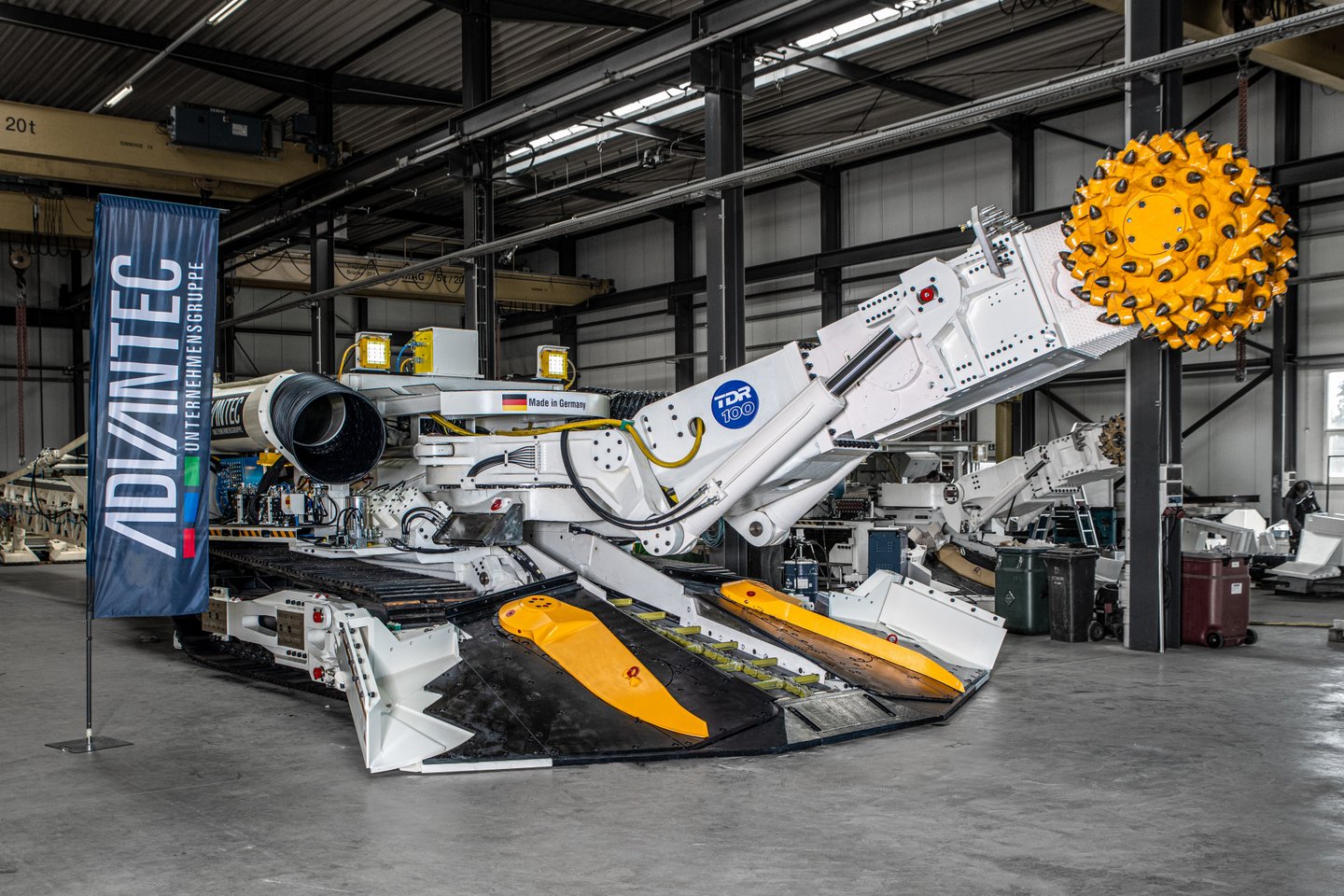
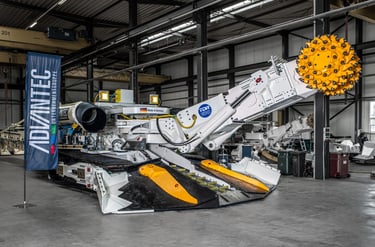
Purpose: Versatile excavators designed for precision rock cutting in tunneling and underground mining.
Technical Features:
Articulating boom with rotating cutting head
Adjustable for precise cutting angles and profiles
Interchangeable cutting picks for different material hardness
Cable Requirements:
Variable geometry accommodation with maintained electrical integrity
Specialized suspension systems to reduce ground contact
Multi-layer protection for repetitive bending stress
EMI shielding for sensitive control systems
Application Focus: Tunnel construction, roadway excavation, and medium-hard rock mining operations.
3. Longwall Shearers
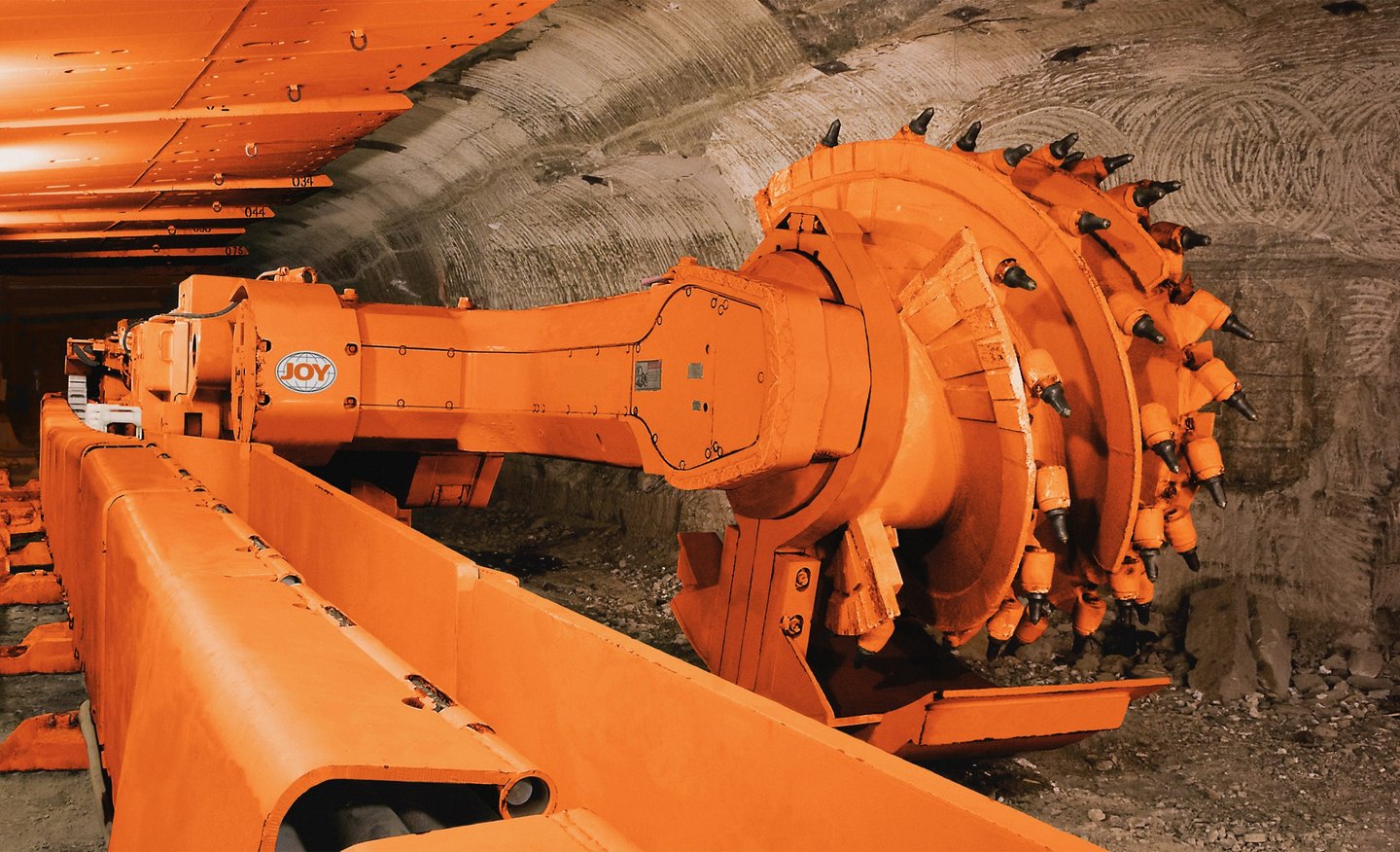
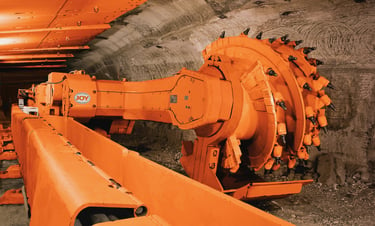
Purpose: High-capacity extraction units that form the core of longwall mining systems.
Technical Features:
Dual rotating cutting drums for efficient material removal
Rail-mounted design for controlled face advancement
Integrated hydraulic roof support coordination
Cable Requirements:
Heavy-duty tensile load capacity
Dynamic tension control systems
Protective armoring against rock face contact
Enhanced shielding for high-power motor applications
Application Focus: Large-scale coal face extraction in longwall panel systems.
4. Drum Cutters
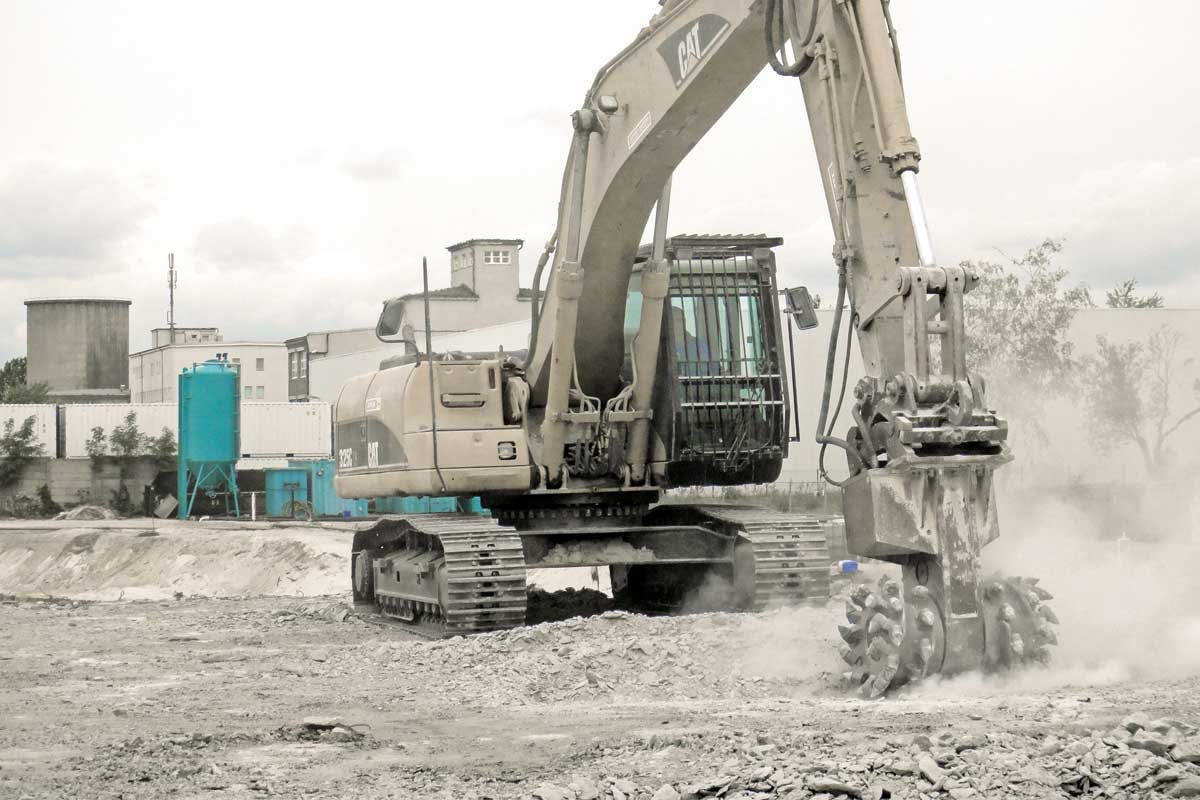
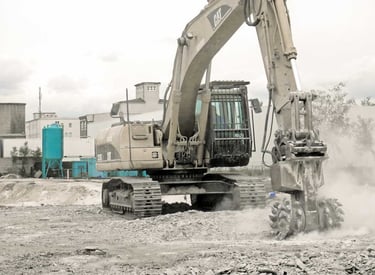
Purpose: Compact cutting attachments that offer precise rock or soil profiling.
Technical Features:
Rotating drum with carbide-tipped teeth mounted on excavator arms
Modular tool configurations for different material types
Low-vibration design for controlled excavation
Cable Requirements:
Protection against localized abrasion points
Sharp-radius bend tolerance for equipment articulation
Quick-disconnect systems for attachment changes
Abrasion-resistant outer jacketing
Application Focus: Tunneling, trenching, and scaling operations in mining and construction.
5. Surface Miners
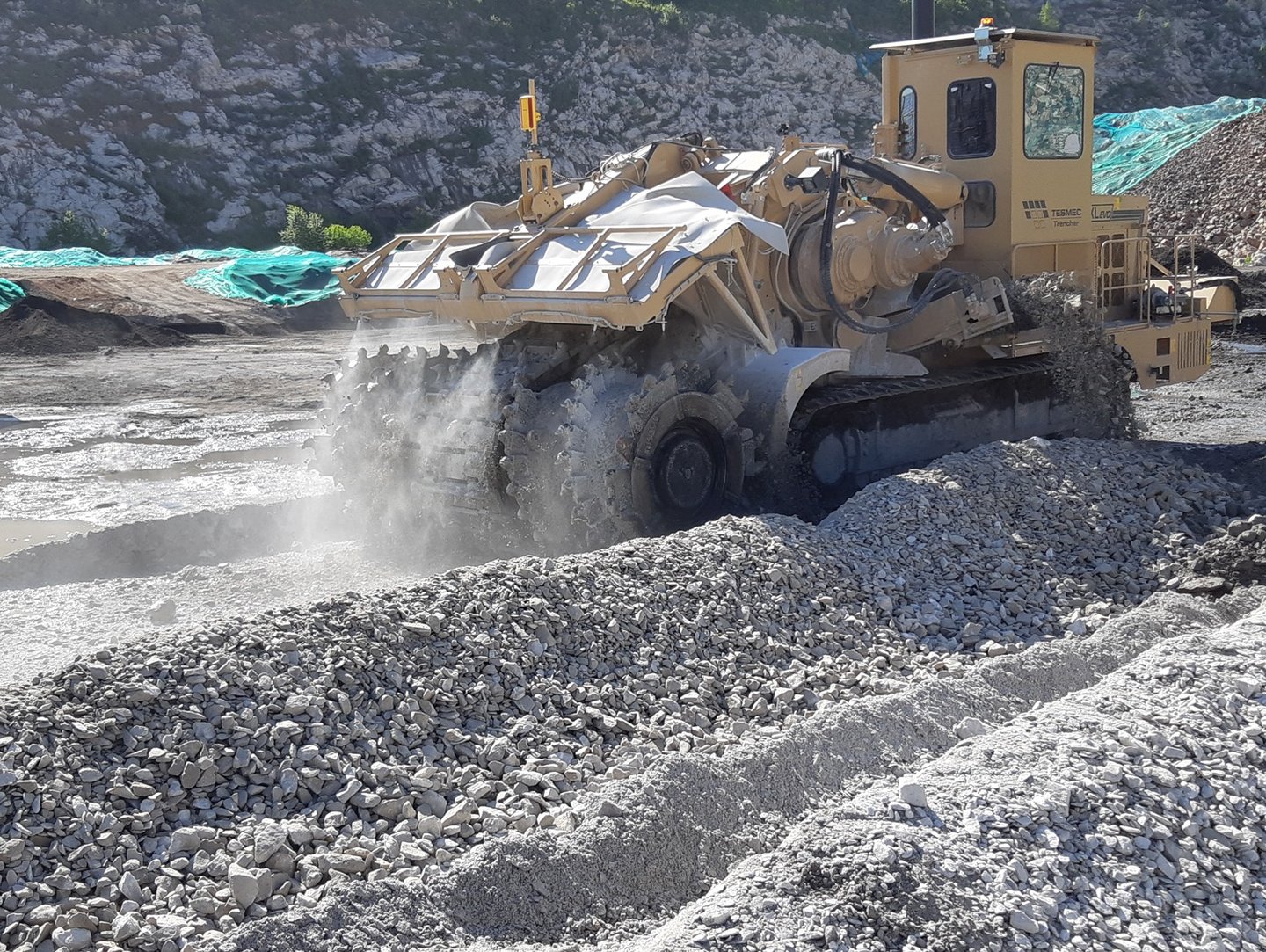
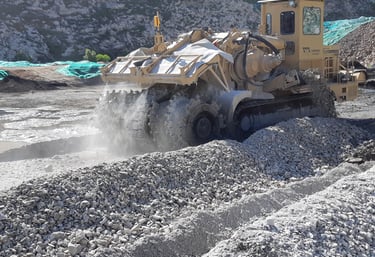
Purpose: Open-pit extraction machines that combine cutting, crushing, and loading functions.
Technical Features:
Massive cutting drum with specialized teeth patterns
Integrated material size control and conveyance
High-durability components for continuous operation
Cable Requirements:
Long-span bend support with minimal strain
UV and environmental exposure protection
Heavy-duty strain relief for substantial power demands
Dust-resistant connector interfaces
Application Focus: Limestone, coal, gypsum, and iron ore extraction in surface operations.
6. Tunnel Boring Machines (TBMs)
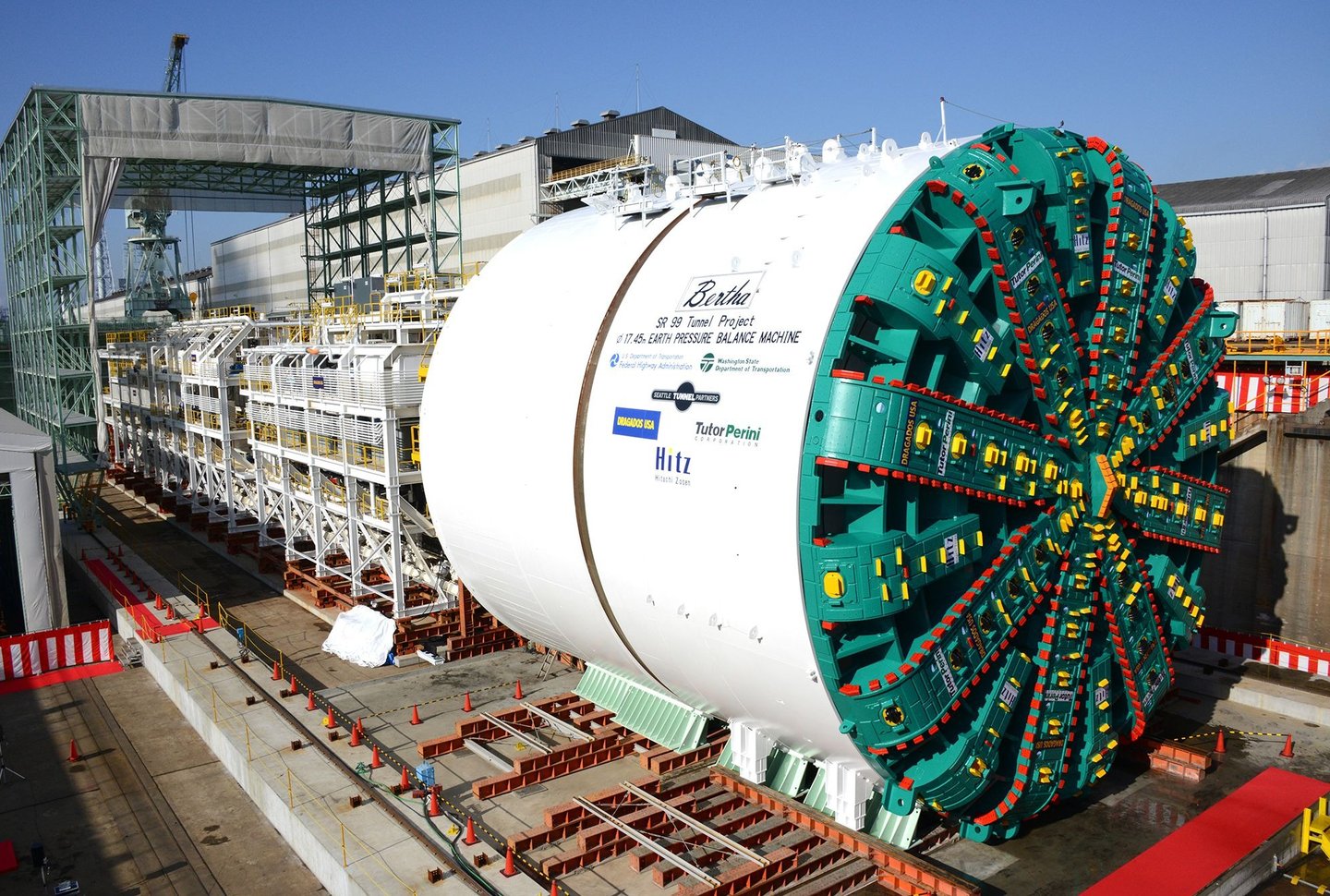
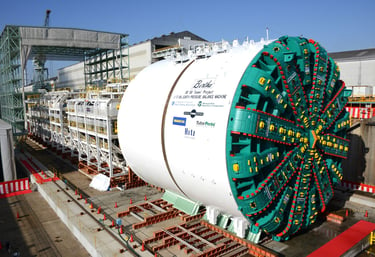
Purpose: Large-diameter tunnel construction systems for both soft and hard rock applications.
Technical Features:
Rotating cutter head with disc cutters for rock fragmentation
Segment erector systems for tunnel support installation
Advanced guidance and navigation capabilities
Cable Requirements:
Extended cable trains with multi-point support
Water and pressure resistance for wet tunneling
Remote routing systems with centralized monitoring
High-flex material compounds for continuous operation
Application Focus: Major infrastructure tunneling and mine access development.
7. Bolter Miners
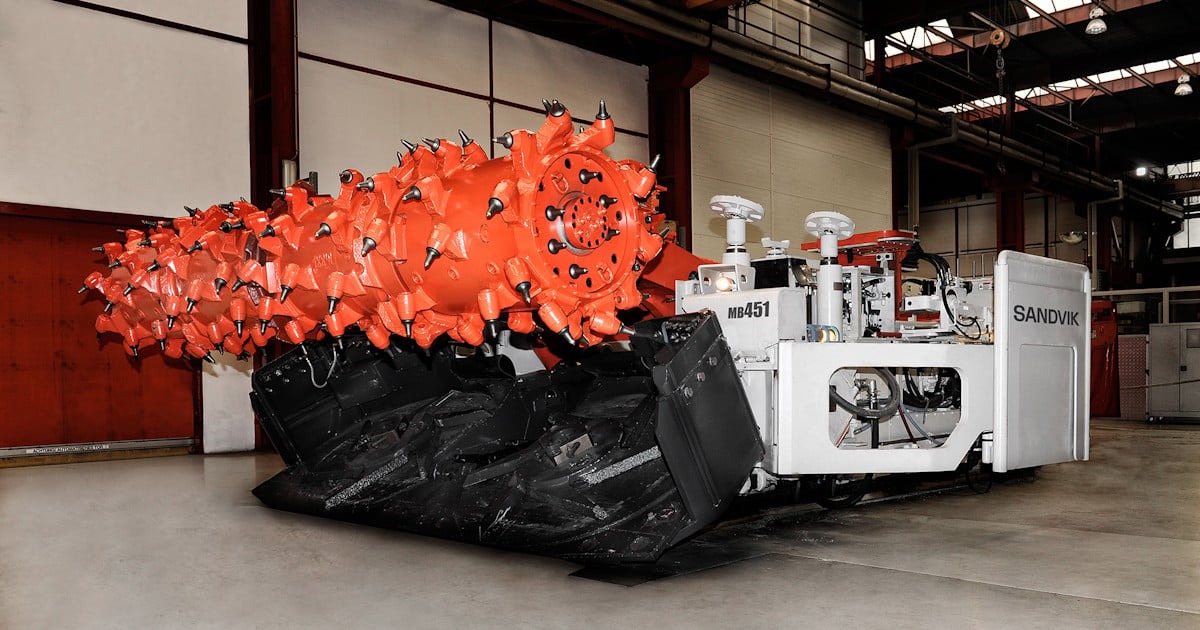
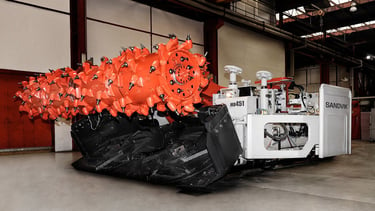
Purpose: Combined excavation and roof support systems for single-pass mining.
Technical Features:
Integrated cutting head and roof bolting equipment
Resin injection systems for immediate ground control
Dust suppression technology for improved safety
Cable Requirements:
Abrupt stop/start cycle tolerance
High-flex joint protection at articulation points
Fire-resistant jacketing for coal applications
Reinforced connection points for operational vibration
Application Focus: Underground coal or soft rock mining requiring immediate roof support.
8. Chain Cutters
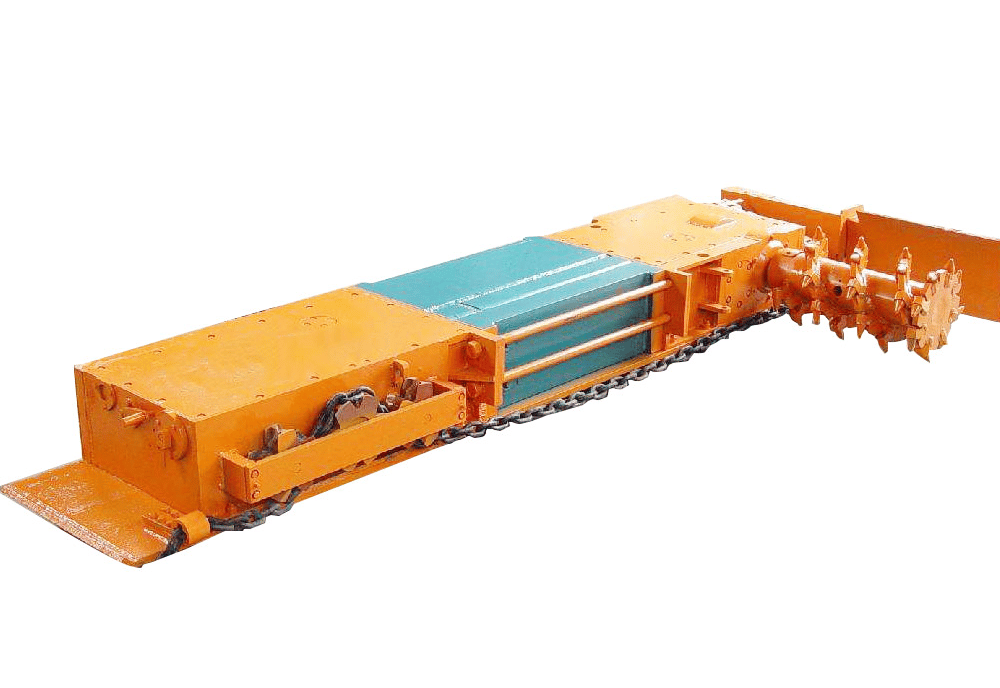
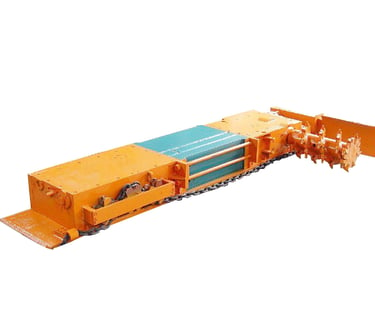
Purpose: Precision tools for extracting thin seams or specific stratigraphic layers.
Technical Features:
Chainsaw-style cutting mechanism with replaceable teeth
Lightweight frame for manual positioning
Variable chain speed for different material hardness
Cable Requirements:
Superior flexibility for operator-guided movement
Small-radius bend tolerance without electrical compromise
Abrasion protection at guide contact points
Lightweight design without sacrificing durability
Application Focus: Selective mining in confined spaces and thin coal seam extraction.
9. Rock Saws
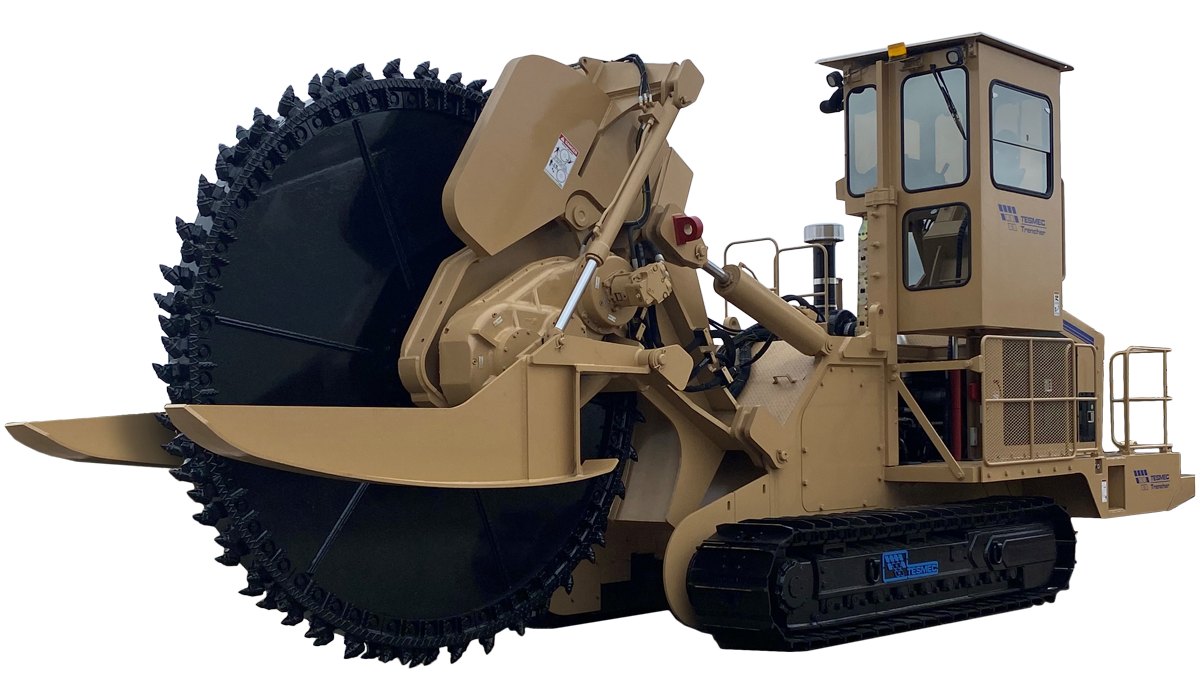
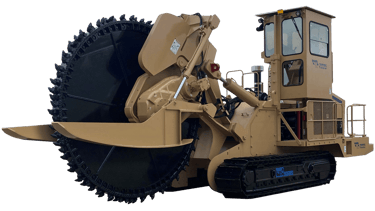
Purpose: Precision cutting tools for dimensional stone and specialized mining applications.
Technical Features:
Diamond-tipped circular blades for clean cutting
Water cooling systems to manage heat generation
Frame stabilization for precise cut control
Cable Requirements:
Water ingress protection with sealed connector systems
Torsional load resistance for blade rotation forces
Reinforced insulation against wet operating conditions
Chemical resistance for coolant exposure
Application Focus: Quarrying, dimension stone extraction, and precision mining operations.
10. Water-Jet Cutting Machines
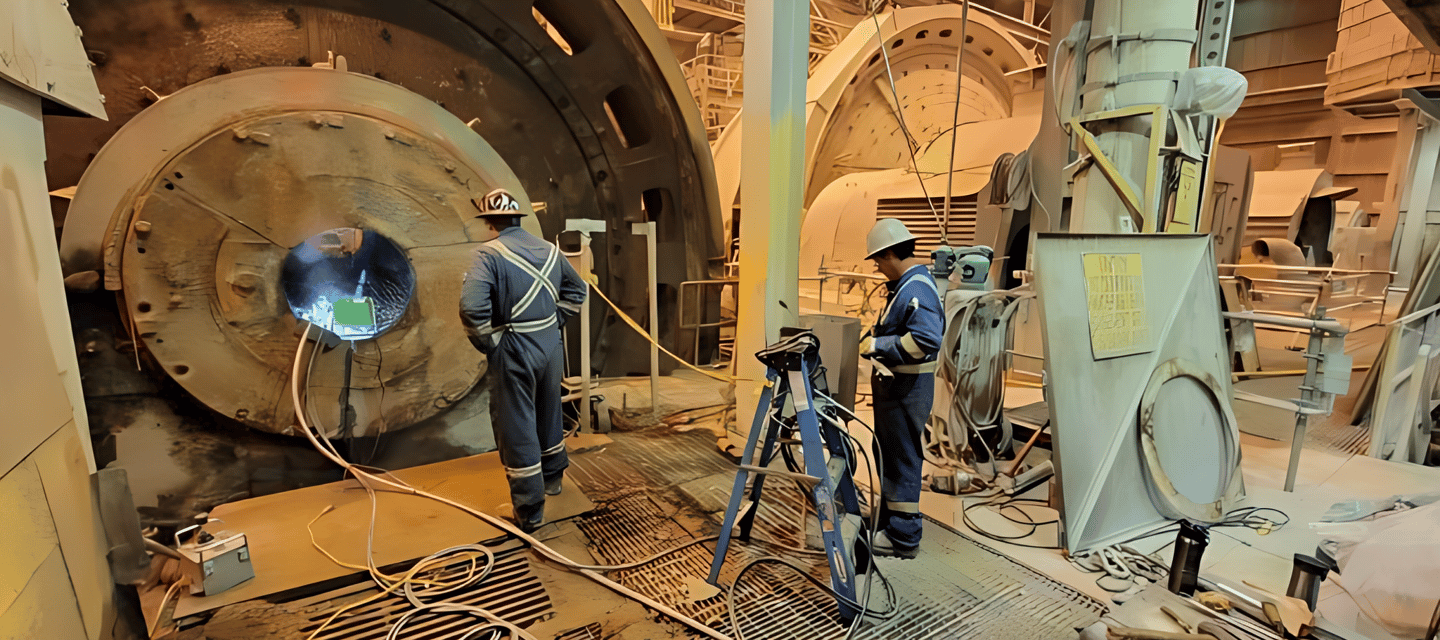
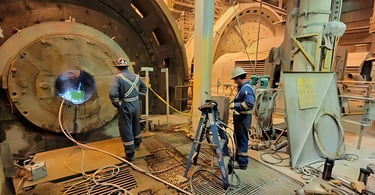
Purpose: Non-thermal, non-spark cutting systems for sensitive or hazardous materials.
Technical Features:
High-pressure water pumps (up to 60,000 psi)
Abrasive mixing for enhanced cutting capability
Remote-controlled cutting head for operator safety
Cable Requirements:
Hydrostatic pressure resistance for submerged operation
Abrasion protection against water/abrasive slurries
Chemical-resistant jacketing for various water treatments
Multi-conductor design for complex control functions
Application Focus: Coal extraction in methane-rich environments and other explosion-sensitive contexts.
11. Auger Miners
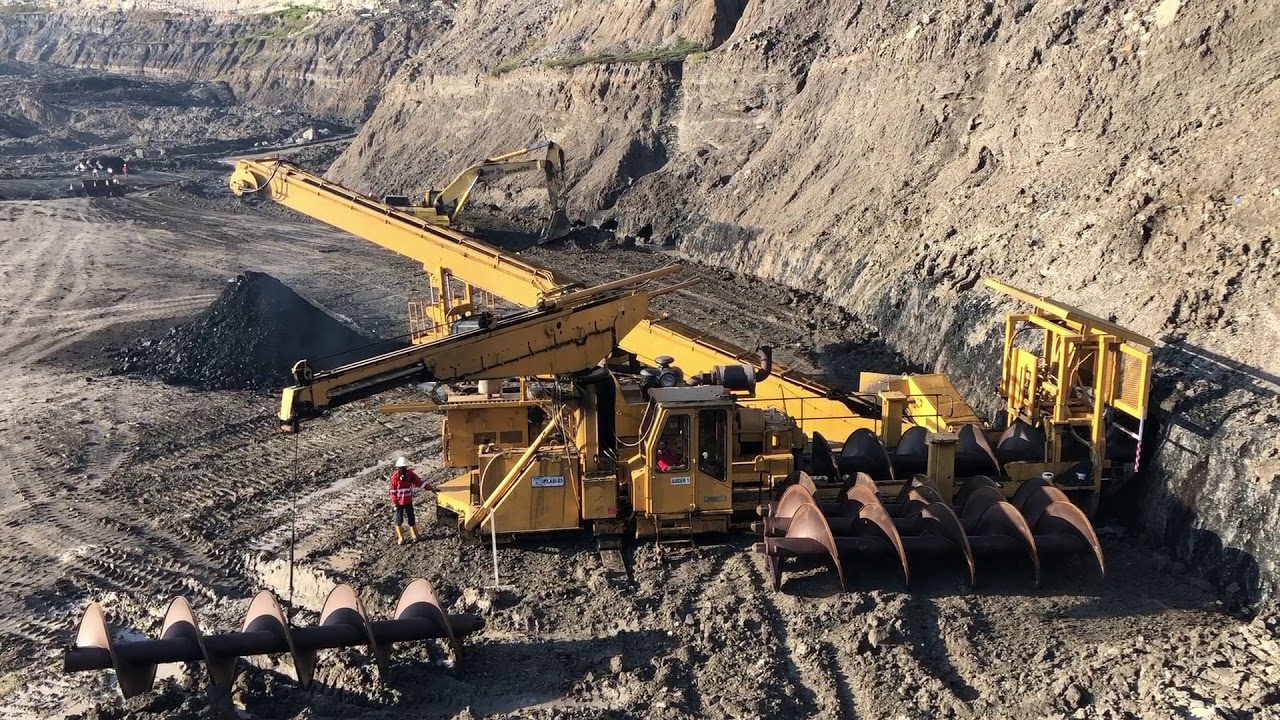
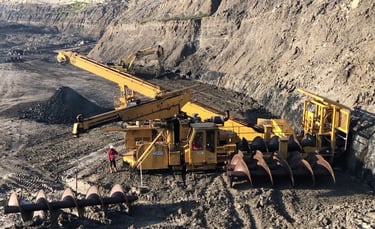
Purpose: Horizontal seam extraction using helical cutting and conveying technology.
Technical Features:
Continuous flight auger for simultaneous cutting and material removal
Sliding shoe guides for controlled penetration
Compact design for remote seam access
Cable Requirements:
Torsional stress resistance for auger rotation
Confined-space routing capabilities
Low-temperature flexibility for various climates
Dual-rated electrical/mechanical specifications
Application Focus: Surface or highwall coal mining in horizontal or slightly inclined seams.
12. Rock Excavation Robots
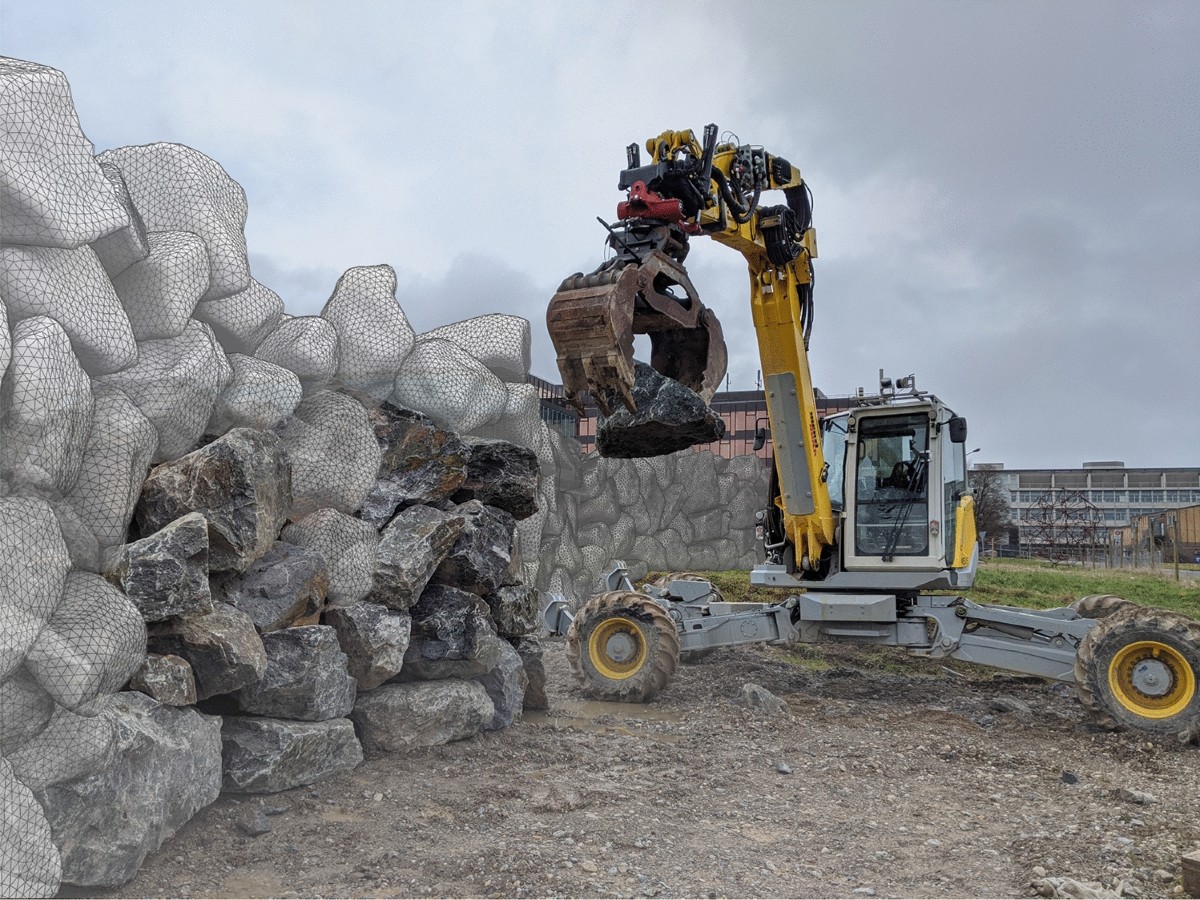
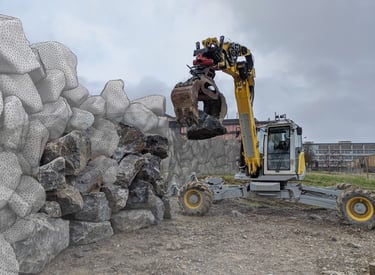
Purpose: Remote-controlled or autonomous cutting systems for hazardous environments.
Technical Features:
Multi-axis robotic arms with specialized cutting tools
Advanced sensor packages for navigation and material detection
Modular design for different cutting attachments
Cable Requirements:
Frequent coupling/decoupling durability
Multi-core designs with integrated signal and power conductors
Enhanced EMI shielding for sensitive control systems
Reinforced armor for unpredictable movement paths
Application Focus: Hazardous zones, unstable ground conditions, and hard-to-reach mining locations.
Technical Considerations for Cable Integration
Abrasion Resistance
The constant movement of mining equipment creates significant abrasion challenges for trailing cables. Modern designs incorporate:
Advanced polymer compounds with high abrasion indices
Braided protective sleeving at identified wear points
Aramid fiber reinforcement in high-stress applications
Removable protective covers for maintenance access
Flex Life Optimization
Cable flex life directly impacts operational continuity and safety. Key considerations include:
Stranded conductor designs with optimized lay lengths
Specialized insulation materials with superior flex memory
Validated minimum bending radius specifications
Cyclic fatigue testing under simulated mining conditions
Tensile Load Management
Different cutting machines exert varying tensile forces on their power cables:
Reinforced strain relief connections at machine interfaces
Internal strength members sized to specific machine pull forces
Load-distributing jacket designs to prevent conductor stress
Tension monitoring systems for preventive maintenance
Thermal Management
Heat generation impacts both cable lifespan and safety:
Temperature-rated insulation materials appropriate for application
Ventilated cable carrier systems for improved heat dissipation
Strategic routing to minimize exposure to motor and friction heat
Thermal imaging as part of routine maintenance protocols
Selection Criteria: Matching Machines with Cables
Proper cable selection requires careful evaluation of multiple factors:
Environmental conditions (wet/dry, abrasive, temperature extremes)
Machine mobility patterns (linear, circular, multi-axis)
Production rate and duty cycle requirements
Material hardness and its impact on machine vibration
Operational speed and resulting flex-cycle frequency
Maintenance access considerations for cable replacement
Regulatory compliance for specific mining environments
Installation Best Practices
Pre-Installation Inspection
Before deployment, cables should undergo:
Visual examination for shipping damage
Verification of sheath integrity
Conductor continuity testing
Insulation resistance measurement
Dimensional compliance checking
Strategic Routing
Proper cable management systems significantly extend service life:
Engineered cable trays with appropriate support spacing
Overhead festoon systems for suspended operation
Floor troughs with abrasion-resistant liners
Articulated cable carriers for complex movement patterns
Strain Relief Implementation
Critical protection at machine connection points includes:
Spring-loaded tension devices
Automated cable retractors for slack management
Load cells for continuous tension monitoring
Pivoting connection points to maintain optimal bend radius
Maintenance and Testing Protocols
Routine Inspection
Regular examination should include:
Visual checks for jacket damage
Sheath thickness measurement at wear points
Resistance testing for early degradation detection
Connection point inspection for thermal stress
Non-Destructive Evaluation
Advanced testing methods provide early warning of developing issues:
Ultrasonic flaw detection for internal damage
High-voltage spark testing for insulation integrity
Thermal imaging for hot spot identification
Partial discharge analysis for insulation degradation
Conclusion
The demanding environments of modern mining operations require cutting machines that combine robust performance with operational reliability. The trailing cables that power these systems represent a critical component that must be carefully selected, properly installed, and diligently maintained. By understanding the specific requirements of each cutting machine type and implementing appropriate cable management strategies, mining operations can maximize productivity while enhancing safety and equipment longevity.
For project-specific cable system solutions, consult with specialized engineering teams who can provide custom jacketing, armoring, and on-site support tailored to your unique mining environment.
This article was prepared by experts in mining equipment and electrical systems to provide technical guidance for engineers, maintenance crews, safety officers, and cable specialists working with mining cutting machinery.
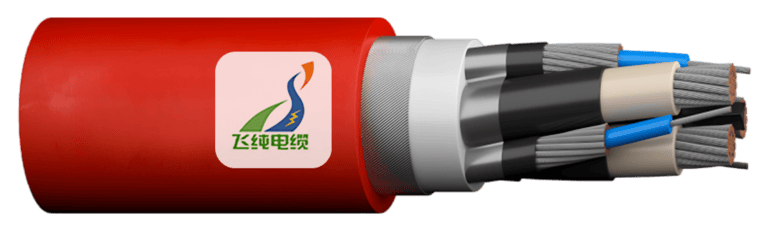
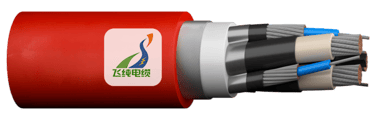
Reeling Cable
Technical insights on flexible power cables for mobile machinery.
Mobile Machinery
Power cables for high-stress operations in ports.
Energy Supply
Flexible solutions for cable reels and trolley systems.
Mechanical Stress
Durable cables designed for frequent bending and torsion.
Port Terminals
Innovative cable solutions for efficient material handling equipment.