Coal Mining: Which Mining Cables Are Suitable for Use
Discover which mining cables excel in coal-mining environments—covering reeling, trailing, armored, control, and fiber-optic types, plus key standards (MSHA, AS/NZS, IEC) and selection guidelines for abrasion, flame, and flex resistance.
Coal Mining: Which Mining Cables Are Suitable for Use
Coal mining operations demand cables that can withstand extreme conditions while maintaining safety and reliability. From underground shafts to surface operations, the right cable selection can mean the difference between continuous production and costly downtime.
The Unforgiving Environment of Coal Mining
Mining cables face a perfect storm of challenges:
Abrasion from coal dust and rock fragments
Chemical exposure to moisture, oils, and acid mine drainage
Extreme mechanical stress from reeling and trailing operations
Fire hazards requiring strict flame resistance
Potential explosion risks in methane-rich atmospheres
These conditions require specialized cable designs that far exceed standard industrial specifications.
Essential Cable Types for Coal Mining Operations
Reeling Cables
These workhorses power draglines, shuttle cars, and roof bolters. Their construction features:
Polyurethane or CPE sheaths for superior abrasion resistance
High-flex copper conductors designed for thousands of bending cycles
Multi-layer armor to protect against crushing forces
For optimal performance, reeling cables like the (V) NTSKCGECWOEU 3.6/6KV and (VO) (N)TSKCGEWOEU 1.8/3KV should maintain flexibility at temperatures as low as -40°C while handling constant movement without conductor fatigue.
Trailing Cables
Continuous miners, conveyors, and longwall shearers depend on trailing cables that can withstand being dragged across abrasive surfaces. Key features include:
Flame-resistant jackets meeting strict MSHA requirements
Steel or textile armoring for mechanical protection
Enhanced conductor designs to prevent breakage during repeated flexing
The TYPE 7, 7S, 7M, and TYPE 11 0.64/1.1KV cables are specifically engineered for these demanding trailing applications, with the (V) NSSHCGEOEU LWL 0.6/1KV offering enhanced flexibility for longwall mining operations.
Armored Power Cables
Fixed infrastructure requires maximum protection against physical damage:
Interlocked steel tape or wire armor provides exceptional crush resistance
Heavy outer jackets resist environmental degradation
Rated for higher voltages to support substation connections
The (V) NTSKCGECWOEU 1.8/3KV and (V) (N)TSKCGECWOEU 1.9/3.3KV models provide reliable power distribution in both underground and surface mining operations.
Control and Instrumentation Cables
Modern mining operations rely on extensive sensor networks and automation systems requiring:
Multi-core pairs with comprehensive EMI shielding
Low-capacitance insulation for signal integrity
Oil and moisture resistance to maintain communication reliability
The (V) NSSHCGEOEU NEW 0.6/1KV and (Z) NSSHKCGEOEU 0.6/1KV are specifically designed for these sensitive control applications.
Fiber-Optic Solutions
High-speed data transmission in harsh mining environments demands:
Armored fiber construction
Oil and moisture-resistant buffer tubes
Ruggedized connectors designed for dirty environments
The Type 241.1 and (Z) NSSHCGEOEU 0.6/1KV models incorporate fiber protection systems suitable for critical communication networks.
Navigating Compliance and Standards
Mining cables must meet stringent regulations:
MSHA approval under 30 CFR 18.64 is mandatory for underground coal mines
AS/NZS 2802 certification classifies cables for specific mining applications
IEC standards address flame propagation (60332-1-2) and insulation ratings (60502)
Group IIA explosion-proof requirements apply in methane-prone areas
Models like the EPN 63 0.6/1 kV are specifically certified to meet these critical safety standards.
Technical Selection Guidance
Material Considerations
Outer sheaths require:
Hydrolysis and ozone resistance
UV stabilization for surface operations
Chemical resistance against oils and mine drainage
Abrasion resistance exceeding standard industrial ratings
The (V) NTSKCGECWOEU 3.6/6KV incorporates advanced polymer blends specifically formulated for these harsh conditions.
Mechanical Performance
Focus on:
Minimum bend radius of 10× cable diameter
Stranded conductor designs that distribute flexing stress
Armor thickness matched to machinery pull forces
Embedded strength members for tensile reinforcement
The (V) NSSHCGEOEU 0.6/1KV features optimized mechanical properties to withstand these stresses.
Temperature and Fire Performance
Safety demands:
Continuous operation rating of at least 90°C for power cores
Peak temperature tolerance up to 250°C during short-circuits
Flame-retardant formulations meeting IEC 60332 and MSHA tests
Installation Best Practices
Proper installation significantly extends cable life:
Conduct thorough pre-installation inspections for shipping damage
Test insulation resistance and continuity before deployment
Implement festoon or trough systems to minimize ground contact
Maintain proper support spacing (≤1m) and radius-controlled rollers
Establish regular thermal imaging inspections to detect developing issues
Maintenance Strategies
Proactive maintenance prevents failures:
Regularly measure sheath thickness to track wear patterns
Conduct electrical diagnostics to identify degradation before failure
Use only manufacturer-approved splice kits and repair materials
Document all repairs in comprehensive maintenance logs
Conclusion
Selecting the right cables for coal mining environments requires balancing electrical performance, mechanical durability, and safety compliance. The (V) NTSKCGECWOEU series, including the 1.8/3KV and 3.6/6KV variants, along with the (V) NSSHCGEOEU and TYPE 7 series cables have proven reliability records in the most demanding coal mining conditions worldwide.
By matching cable construction to specific operating conditions, mining operations can optimize uptime while maintaining the highest safety standards. Whether you need the robust performance of the (V) NTSKCGECWOEU 3.6/6KV for high-voltage applications or the specialized capabilities of the (Z) NSSHCGEOEU 0.6/1KV for control systems, today's purpose-built mining cables deliver essential reliability in extreme environments.
Keywords: Coal Mining Cables, (V) NTSKCGECWOEU 3.6/6KV, (V) NSSHCGEOEU 0.6/1KV, TYPE 7 0.64/1.1KV, Mining Cable Standards, MSHA Flame-Resistant Cable, (V) (N)TSKCGECWOEU 1.9/3.3KV, Armored Power Cable, Type 241.1, EPN 63 0.6/1 kV, (Z) NSSHKCGEOEU 0.6/1KV

Frequently Asked Questions (FAQ)
What environmental challenges do coal-mining cables face?
Cables endure intense abrasion from coal dust and rock fragments, chemical attack by moisture and acid mine drainage, extreme mechanical stress from reeling and trailing, and fire/explosion risks in methane-rich atmospheres arlweb.msha.gov.
Which cable categories are essential for coal-mining operations?
Five main types are used: Reeling Cables, Trailing Cables, Armored Power Cables, Control & Instrumentation Cables, and Fiber-Optic Cables nz.prysmian.com.
What defines a reeling cable in mining?
Reeling cables feature durable PUR or CPE sheaths, high-flex copper conductors, and multi-layer armor to withstand constant bending as they wind on and off drums nz.prysmian.com.
What are trailing cables, and where are they used?
Trailing cables power continuous miners, conveyors, and shearers; they require steel/textile armoring and flame-resistant jackets per MSHA 30 CFR 18.64 arlweb.msha.gov.
Why choose armored power cables for fixed infrastructure?
Armored cables use interlocked steel tape or wire armor under a heavy jacket to resist crush and impact in feeder lines and substations 电子联邦法规委员会.
What makes control & instrumentation cables different?
These multi-core cables combine foil/ braid EMI shielding and low-capacitance insulation to maintain signal integrity in sensor and PLC networks Home.
How are fiber-optic cables adapted for coal mines?
Armored fiber-optic cables use oil- and moisture-resistant buffer tubes plus ruggedized connectors to deliver high-speed data in harsh conditions.
Which flame-resistance tests apply to mining cables?
Cables must pass vertical flame propagation tests per IEC 60332-1-2 and meet MSHA 30 CFR 18.64 flame-resistance requirements IEC Webstorearlweb.msha.gov.
What does MSHA 30 CFR 18.64 require?
All trailing cables in underground coal mines must bear MSHA acceptance markings and resist flame per Title 30, Part 18.64 arlweb.msha.gov.
What does AS/NZS 2802 cover?
AS/NZS 2802 specifies construction and testing for flexible reeling and trailing cables used in surface and underground mining applications tratosgroup.com.
What voltage ratings are common for coal-mining cables?
Typical ratings range from 0.6/1.0 kV (control) up to 3.6/6.0 kV (power), with higher-voltage variants for longwall and dragline service nz.prysmian.com.
What is the minimum bend radius for mining cables?
Manufacturers generally specify a minimum bend radius of 6×–10× the overall cable diameter, validated by cyclic-bend tests fy-powercable.en.made-in-china.com.
How is abrasion resistance achieved?
Using advanced polymer blends rated for high abrasion indices, braided outer sleeving, and aramid fiber reinforcement at wear points aein-wirecable.com.
How is flex life optimized?
By selecting stranded conductor constructions with optimized lay-lengths and specialized insulation compounds offering superior flex memory nz.prysmian.com.
Why is tensile management critical?
Reinforced strain-relief terminations and embedded strength members must accommodate specific machine pull forces to prevent conductor overstress nz.prysmian.com.
How do I select sheath materials for chemical exposure?
Choose jackets with proven resistance to oils, hydrocarbons, acids, and alkaline mine drainage—typically CPE or specialized elastomers nz.prysmian.com.
What role does EMI shielding play?
Proper braid/foil shielding protects delicate control signals from high-power motor noise in crowded electrical environments Home.
How often should trailing cables be inspected?
Perform visual inspections monthly, sheath-thickness measurements quarterly, and electrical testing (continuity, insulation resistance) annually Western Australian Government.
What pre-installation checks are mandatory?
Verify reel condition, jacket integrity, conductor continuity, insulation resistance, and dimensional compliance before deployment Western Australian Government.
How should cables be routed in underground workings?
Use festoon systems or floor troughs with abrasion-resistant liners and maintain proper support spacing (≤ 1 m) Western Australian Government.
What maintenance actions extend cable life?
Regular sheath-thickness monitoring, electrical diagnostics, thermal imaging at terminations, and timely repair of worn sections tfkable.com.
How are damaged cables repaired?
Employ MSHA-approved heat-shrink splice kits and over-molded repair assemblies per manufacturer guidelines arlweb.msha.gov.
What is a festoon cable system?
An overhead support arrangement using rollers or trolleys to guide trailing cables and prevent ground abrasion Western Australian Government.
How do environmental conditions affect cable choice?
Wet, dusty, or chemically aggressive atmospheres demand specialized sheaths and sealing to prevent premature failure Western Australian Government.
What crush-resistance features are available?
Interlocked steel tape or wire armor under a robust jacket protects against impact and rockfall damage 电子联邦法规委员会.
What is LSZH and when is it used?
Low-Smoke Zero-Halogen jackets minimize toxic gas emission during fires, often specified for underground public access areas Power and Cables.
How are intrinsic-safety requirements met in methane zones?
Cables in Group IIA atmospheres must use flame-proof enclosures and special armoring to prevent ignition sources 电子联邦法规委员会.
How do I verify flame performance?
Conduct vertical flame tests per IEC 60332-1-2 and full-scale cable bundle tests per IEC 60332-3-22 IEC Webstore.
What testing standards govern insulation ratings?
Insulation systems typically conform to IEC 60502 for power cables and relevant EN/IEEE standards for control cables IEC Webstore.
How is cable flexibility measured?
Flexibility is assessed via cyclic-bend machines running thousands of cycles at specified radii and temperatures nz.prysmian.com.
What PPE is required when handling mining cables?
Use insulated gloves, dielectric boots, arc-rated clothing, and face shields when working near energized cables arlweb.msha.gov.
How should live cables be isolated during maintenance?
De-energize lines per lock-out/tag-out procedures or use insulated barrier hoses when power cannot be removed 电子联邦法规委员会.
How do I document cable maintenance activities?
Maintain detailed logs of inspections, repairs, tension readings, and test results to support audits and warranty claims Western Australian Government.
Which cable models are MSHA-approved for underground coal?
Models such as MP-GC, NTSKCGECWOEU series, and TYPE 7/11 variants carry MSHA 30 CFR 18.64 acceptance for power and trailing cables nz.prysmian.com.
How can I get custom cable solutions for coal mines?
Feichun Cable offers tailored designs in sheath compounds, armoring, and multi-core arrangements—contact our engineering team for project-specific recommendations.
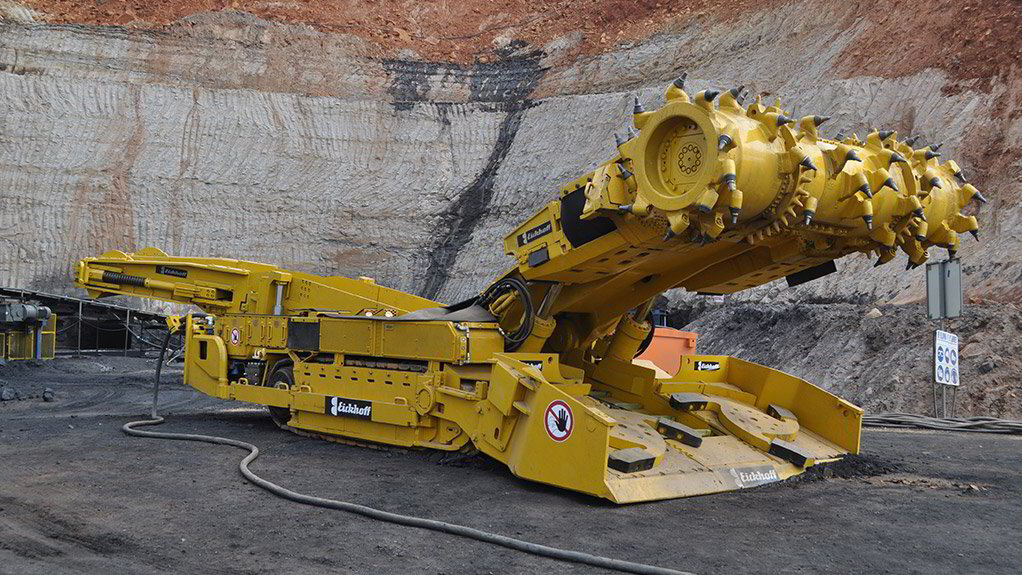
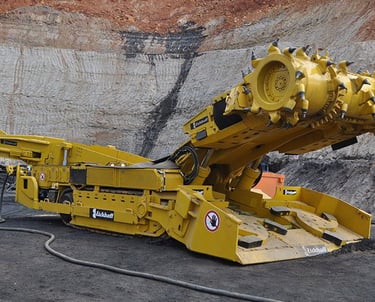
Coal Mining: Which Mining Cables Are Suitable for Use
Discover which mining cables excel in coal-mining environments—covering reeling, trailing, armored, control, and fiber-optic types, plus key standards (MSHA, AS/NZS, IEC) and selection guidelines for abrasion, flame, and flex resistance.
4/30/20257 min read